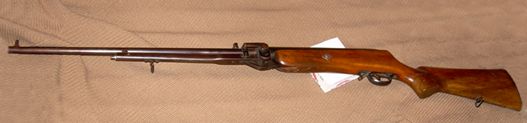
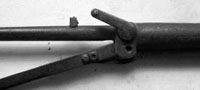
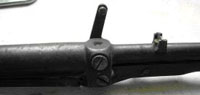
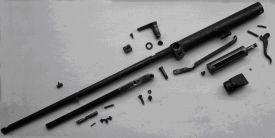
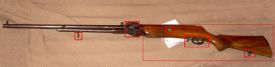
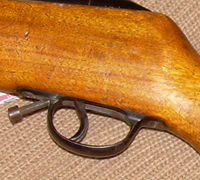
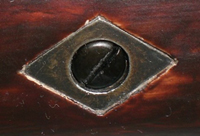
Lo primero que hizo fue buscar fotos de alguna unidad completa para ver qué le faltaba a la mía. Y para ello, se sirvió de la foto publicada en la web de José Manuel más la que le hizo a la suya otro gran amigo del gremio que es César (usuario rojocaecae) al cual quiero aprovechar para agradecérselo públicamente. Además, se da el caso de que la de César es el mismo modelo que la mía con la apertura del puerto de carga automático. Comparadas las carabinas, parecía obvio que faltaban muchas piezas que habría que fabricar, incluida la culata. En este sentido, siempre he dicho que el trabajo de Nicolás se parece mucho a la anatomía comparada de la paleontología, ya que tiene que fabricar piezas que debe imaginarse como son con solo ver las de alrededor y sus movimientos.
La culata fue adaptada a partir de otra vieja de un modelo similar. Se fabricó y se incrustaron las piezas metálicas en forma de rombo, justo donde se alojan los tornillos de fijación. También se hizo un cuero de cazoleta especial para ella, pues la medida interior del diámetro de la cámara es superior a las que existen actualmente. Incluso tuvo que fabricar un muelle especial, pues no hay nada en el mercado actual que se adapte a la cámara de potencia de la Symba. Nicolás se encontró también con que el diámetro interior de la cámara era de 28 mm, en vez de los 25 que suelen tener, por lo que no servía ninguno de los cueros que tenía, ni los que encontró a la venta. Tenía que fabricar uno a medida. Como los restos del cuero viejo eran los de un cuero de “cazoleta", decidió hacer uno de este tipo.
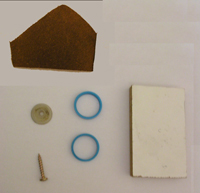
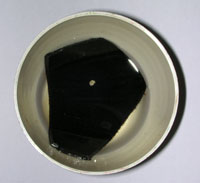
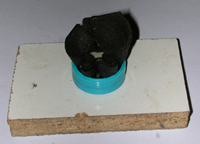
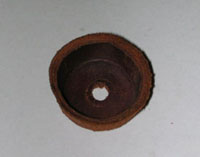
- Un trozo de cuero de unos 3mm de espesor.
- Dependiendo de la altura que se le quiera dar, uno o dos aros o anillos con el mismo diámetro interior que el de la cámara.
- Otra pieza con un diámetro igual al interior de los aros, menos dos veces el grosor del cuero, aproximadamente. En este caso, 22mm de diámetro.
- Un tornillo tirafondo. También vale con rosca.
- Un trozo de madera.
Una vez reunidas todas las piezas, primero se perfora el cuero haciendo un orificio del diámetro del tornillo que lo va a sujetar al émbolo. A continuación se sumerge en aceite, muy fluido, tipo 3 en 1 o similar, y se deja que se empape bien durante uno o dos días. Si el aceite se tiñe del color del cuero, hay que cambiarlo. Esto significa que se están disolviendo los taninos del cuero y entonces el cuero se degrada, se vuelve menos flexible y tiene más posibilidades de romperse. Lo mas rápido es con agua, pero la disolución de los taninos es segura. Hay que sacarlo antes de que se disuelvan y luego hay que acelerar el secado y aceitarlo, con lo que prácticamente no se adelanta nada.
En la tabla, perforamos un agujero de un diámetro algo menor que el del tornillo e igual de largo. Colocamos los aros, la pieza y el tornillo tal como se ve en la siguiente foto. A continuación, introducimos el tornillo en el agujero de la tabla y atornillamos despacio, poco a poco, ayudando con las manos a que el cuero entre dentro de los aros. Seguimos atornillando hasta llegar al tope, es decir que el cuero quede comprimido contra la tabla. Si el tornillo es mayor que el grueso de la tabla, hay que tener cuidado al final de atornillar porque podemos estropear la mesa y si es la de la cocina u otra similar… no os imagináis como se pone la jefa de personal.
Una vez que hemos terminado de atornillar, se deja secar y con un cúter o cuchilla se corta a ras de los aros como en la foto siguiente. Cuanto más seco, mejor se corta. Después, con unos alicates, se quitan las ondas que hayan quedado, con cuidado, no hay que apretar mucho. Esta operación solo será necesaria en el caso de que la pieza interior sea más corta que los aros y habrá que realizarla más de una vez hasta que se seque. Después, se deja secar el tiempo que sea necesario. Después de seco, se quita el tornillo y los aros lo recortas y perfilas bien, si es posible, dándole una ligera inclinación hacia dentro, y tienes el cuero terminado. Habrá que engrasarlo a la hora de ponerlo. Lo mejor es ponerlo nada más sacarle de los aros.